Le salon des Solutions
environnementales du
Grand Est
Les Actualités
En Alsace, Keey Aerogel recycle des déchets du bâtiment pour produire de la silice
14/06/2024
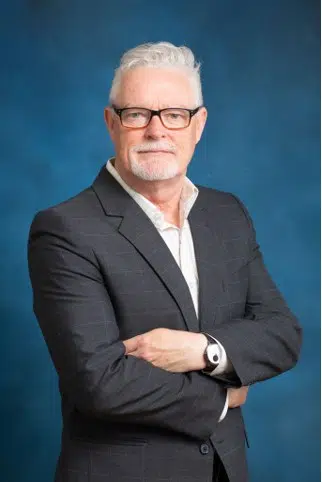
Soutenue par BPIFrance, Capital Grand Est et Innovation Fund (Belgique), Keey Aerogel est une jeune entreprise de production de silice grâce à un procédé de recyclage des déchets du bâtiment.
Actuellement basée en Alsace à Habsheim, à 20 kilomètres de Bâle (Suisse), Keey Aerogel compte 12 salariés et prévoit sur 2024 un chiffre d’affaires de plus de 2 millions d’euros. Michael O’Connor, directeur général et responsable ‘business développement’ est un ancien salarié d’un des leaders états-uniens de la silice et a repris du service, convaincu du projet. Il annonce l’installation à venir de la première usine à production continue « dans la région de Mulhouse, sur environ 3 500 mètres carrés« . Si l’emplacement reste à définir, le financement est lui aussi à compléter à hauteur de 30 millions d’euros.
Cette usine devrait permettre de produire entre 5 et 10 millions de mètres cubes de la silice Keey Aerogel. Les principaux clients de l’entreprise sont aujourd’hui la Suisse, l’Italie et la France. Les nombreuses applications du matériau « promettent une croissance exponentielle de l’activité« , s’enthousiasme le directeur général et responsable du développement. Parmi ces applications, une très en vogue : l’isolation thermo-réfractaire des batteries de voitures électriques. Concrètement, si une des batteries de l’ensemble chauffe, la silice empêchera le suréchauffement des voisines. Les autres applications se situent dans le bâtiment et l’industrie, notamment la pétrochimie.
98 % d’air et un modèle intégral
La silice produite par Keey Aerogel a pour particularité de provenir des déchets du secteur du bâtiment, même de l’amiante. Le recyclage de ces matériaux en silice est la première partie de la boucle imaginée par l’entreprise L’eau et l’éthanol utilisé pour la transformation du produit est recyclé à 99 %. Et le matériau final contient 98 % d’air et 2 % de silice qui peut également être recyclé. « Il faut ajouter à cela la future usine entièrement pensée autour de la réduction de l’impact environnemental et des coûts de production et nous sommes sur un modèle pensé propre dans son intégralité« , expose Michael O’Connor.
Si la première usine prendra place à Mulhouse pour augmenter la production, les suivantes seront éclatées à travers l’Europe. Là aussi dans une optique de réduction d’un impact : celui du transport.
Marine Dumeny / journaldelindustrie